This item has been supplied by a forage marketer and has not been edited, verified or endorsed by Hay & Forage Grower. 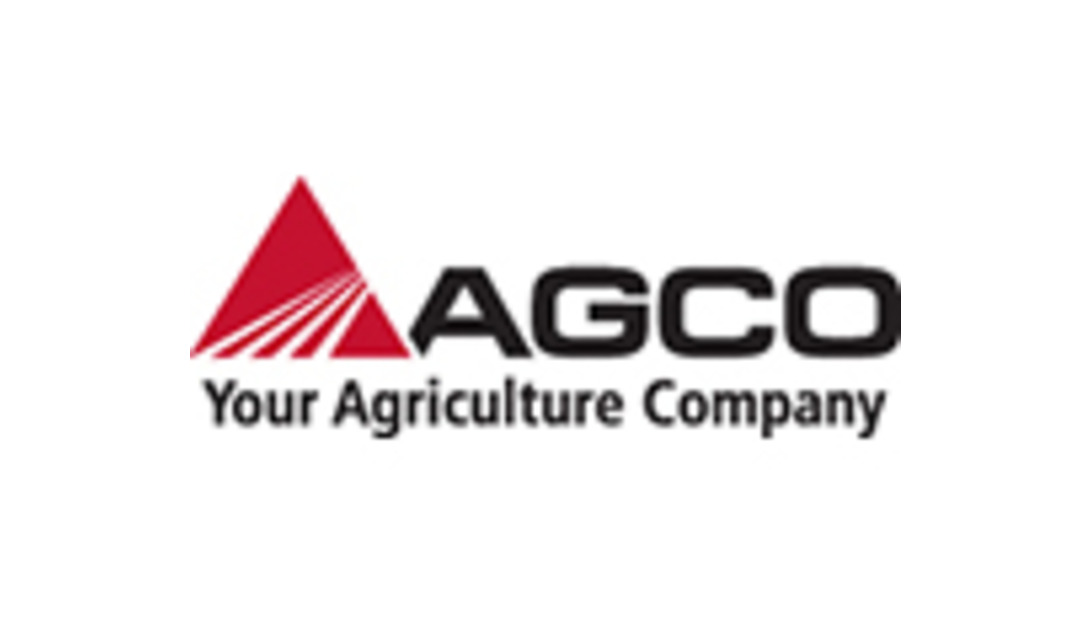
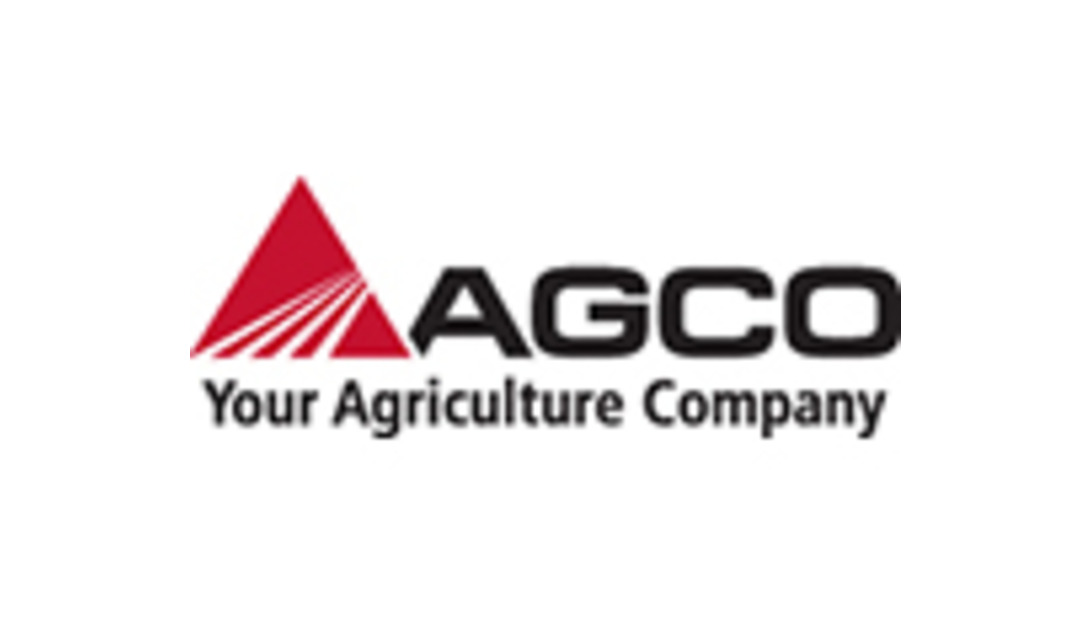
AGCO Corporation(NYSE:AGCO), a worldwide manufacturer and distributor of agricultural equipment, announces farm equipment dealerships in 11 Western states will now receive parts service from a newly opened AGCO Parts facility in Visalia, Calif. The larger, more centrally located parts distribution center (PDC), will provide an expanded offering of parts to customers throughout the Western states and improved parts delivery time, particularly within California. To mark the official opening, AGCO Parts dealer representatives from throughout the Western United States toured the facility Feb. 13, 2017, during Grand Opening activities.
“There’s nothing more frustrating than an equipment breakdown when time is of the essence and a valuable crop is on the line,” says Joe DiPietro, vice president and general manager, AGCO Parts Americas. “We understand our customers and technicians need the right parts quickly, to get equipment back into the fields.
“Relocating our western-most parts distribution center to Visalia improves ground shipping to dealers within California, and the larger facility allows us to keep even more parts on hand. These things help us provide the right parts at the right time and ensure our dealers keep customers’ equipment running smoothly, while providing the superior service customers expect,” DiPietro adds.
AGCO Parts western region distribution center was moved from Stockton, Calif., to a larger facility in Visalia. The new PDC has increased capacity of 33 percent compared to the previous location, permitting an increase in inventory value of 41 percent. The Visalia facility will provide service to 132 dealer locations throughout Arizona, California, Colorado, Hawaii, Idaho, Montana, Nevada, Oregon, Utah, Washington and Wyoming.
Reduced Shipping Timeline
By relocating to the Visalia facility, closer to the nearby UPS shipping hub, AGCO Parts can now provide one-day shipping to 98 percent of dealers within California. And one-day shipping can be guaranteed to other locations for orders placed according to AGCO Parts’ shipping terms and conditions. The central location also makes on-site parts pickup of in-stock items more feasible for customers or dealers during critical production times when getting equipment repaired and back into the field is vital. The larger facility also was carefully stocked, after thorough research into region-specific needs based on customer equipment inventory.
In addition to a 14 percent increase in the number of individual products kept in stock, additional powered industrial equipment and storage racking were purchased to fully utilize the facility’s expanded size and volume.
Parts are stocked at the facility for Challenger®, Massey Ferguson®, Fendt®, Gleaner®, Hesston® by Massey Ferguson, White Planter™ and Sunflower® brand equipment, as well as RoGator® and TerraGator®. The facility will stock parts from other equipment brands offered through AGCO, and parts for AGCO Legacy brands also may become available.
New Western Regional Training Center Delivers Advanced Education
The additional square footage at the Visalia PDC enabled AGCO to open the Western Regional Training Center in the same location. Training is now being conducted for dealer service technicians, as well as their sales and parts personnel on all products and services from AGCO, including Massey Ferguson high horsepower, mid-range and utility tractors; Challenger track and articulated four-wheel drive tractors; commercial hay and hay tools; and a variety of other products.
“Offering state-of-the-art training and information to help technicians within the AGCO dealer network successfully diagnose and repair equipment for customers is a top priority for AGCO,” says Kent Butler, vice president of Technical Services and Support. “Hosting training so close to our dealers in this region will help them reduce travel time and costs, and minimize lost production time. The new Visalia PDC and training facility is just one example of our intensive efforts to ensure the success of our western dealers.”
Planning for the Western Regional Training Center began in 2015 and was a collaboration between teams from AGCO’s Service and Parts divisions. The training center was modeled after a previous collaboration that paired a parts distribution center and regional training center in Woodstock, Ontario. Regional training centers build upon AGCO’s commitment to educate dealers and employees, which kicked off in 2011, with the opening of the AGCO Global Learning Center in Atlanta and AGCO Academy with its seven schools of dealer-focused learning.
For more information about AGCO Parts, its products, services and in-season promotions visit AGCOParts.com.