Ag-Xcellence has their Baler Performance Monitor model BPM-101 on the market for any small square baler new or old. The monitor includes a Stroke/Flake Counter that can help you keep a consistent bale length and weight by counting the number of strokes or flakes in your bale.
Counting flakes is important to keep balers as productive as possible. This unit can display in- chamber hay moisture via optional Single or Dual Moisture Sensor Pads for one or both sides of the bale. This is a time saver for knowing if conditions are changing without having to stop to check. Our product also has a GPS ground speed sensor option that allows baler operators to know approximately how fast to go for conditions and to get back to the correct speed when turning around. By having all this data in one monitor it reduces the number of monitors in the cab.
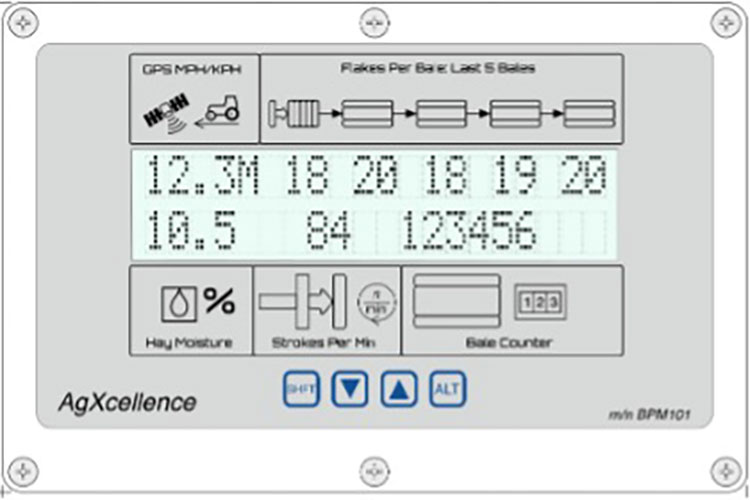
Flake Counter
How does a flake counter benefit hay producers? And what can it do for you? It allows a baler operator to make bales of more consistent length and weight.
Most hay retailers and consumers at the very least appreciate bales of the same weight and length, but many demand it, sometimes with contracts. But let's think back to the beginning of putting up a cutting of hay, first you must choose when to cut in between storms, then get the hay to cure, usually with some combination of tedding and raking, now it’s time to bale and after getting a square baler to tie properly…. you now need to get the bales out of the field! While removing and stacking bales by hand doesn’t mind bales of different length within reason, (never mind your back or labor cost) the mechanical bale handling systems all work better with consistent length and consistent weight. Consistent bales can help make stacks more stable and less likely to fall apart due to the lack of differing lengths and weight distribution.
Without a flake counter small bale producers count flakes by starting to count after the knotter ties, counting each time the plunger compresses hay and then start over when the knotter ties again. The number counted just as the knotter trips is the flake count for the last bale. If you are unsure if a flake counter can help you, try counting manually to see the benefits.
Knowing the bale flake count allows an operator to have a flake count target, if the target number is not correct the operator can adjust his speed accordingly. Higher flake count means the ground speed is too slow, lower flake count means too fast. When the ground speed of the baler is adjusted to maintain the same flake count per bale despite the hay yield (tonnage/thickness) changes in the field, the bale weight and length of each bale are consistently close to each other. This is because hay flakes of different sizes compress at different rates, small flake compress tighter and large flakes want to spring apart. By keeping the same sized flakes, the knotter can tie at the same length and the amount of hay being compressed stays the same leading to consistent bale weight.
If you don’t have a flake count target in mind an easy way to determine one is to pick a flake size of 2-4 inches and divide your desired bale length by the flake size. Example: 36-inch bale length/ 3-inch flake size=12 flakes per bale another example is: 45/3=15. The target doesn’t have to be exactly what was calculated but within 1-2 flakes is good.
Another benefit of using flake counters is it helps keep balers more productive. This is accomplished by keeping the flakes per bale the same even though the tonnage per acre changes. For example, if the field is producing 2-ton per acre in one area but maybe only 1 ton in another you can double your ground speed in the 1-ton area to keep your flake count the same and your tons per hour the same and double your acres per hour. By not overfeeding the baler you can also increase your productivity by not braking twine or knots. When hay is overfed into the baler it can cause the twine to come out of the twine holder making the knotter mis-tie. Or if the bales are too springy from overfeeding for conditions (very dry hay, less than 10%) it can cause tension breaks in the twine. Bales with low flake count tend to be soft and loose, making for poor stacking. The less bales you have to re-bale, or the less time spent unplugging your baler the more productive you will be. Flake counters are a great tool for new baler operators and experienced operators like the convenience of not counting manually.
As monitor displays the flake count of the current bale being made the number increases each time the plunger strokes. When the knotters tie the bale, the final flake count for that bale is shifted to the right allowing you to see the previous bale’s count while the current count increases for the new bale being made. The previous bale counts are displayed for the last four complete bales, this feature is for seeing if the flake count is trending up or down to know if ground speed adjustments are needed. This prevents you from having to watch for each flake count to display and then keep mental notes of the last few bales.
When baling it’s important to not react every time the flake count is not on target, if it’s slightly different don’t change anything for two or three bales and just watch to see if it’s consistently going up or down. If you get a few bales with that are 2-3 flakes off target (all high or all low) change your ground speed to correct it. If the flake count is flipping back and forth from too many or too few by only 1-2 flakes you can keep it right where it is. If it bounces up and down 3- 4 flakes or more slow down to keep the target number about the max number (it’s better to go a little slower than too fast). For most baling you will want to keep your baler at max PTO speed and adjust the transmission to get the correct flake count or as close as you can.
If you are keeping the flake count on target but your bale weight or length is off, make the needed adjustments to the baler and readjust ground speed to maintain the flake count target after each adjustment. The bale length and weight adjustments will affect the flake count, if the tension for weight is too low hay will move though the chamber very quickly and trip the knotter before the target flake count can be achieved. Both the tension and length adjustments will need to be changed for different crops and conditions. The tension may need to be changed to maintain the same weight as moisture changes. Typically grass crops will need higher flake counts because they don’t compress easy, crops like alfalfa compress much more easily and can utilize a lower flake count for higher productivity.
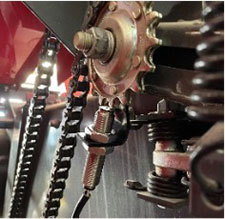
The monitor also displays the strokes per minute rate of the plunger this is useful to know if the tractor PTO speed is correct, and to make sure the slip clutch is not slipping too much. It can also be used to operate a baler (or fleet of balers) at reduced speeds in light crops when the flake count is way too high. It’s handy for checking the efficacy/settings of engine or hydro drive (commonly found on 3-tie) balers.
The monitor also can keep count of your total bale count and can be reset at any time. So, if you want to keep track of totals for a field, the day or the season you can use it how you see fit.
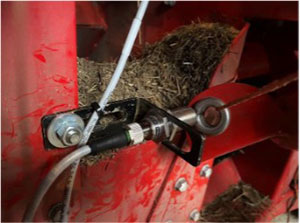
The flake counter works by mounting two sensors with supplied brackets on the baler, one on the knotter idler sprocket for counting plunger strokes and one on the baler frame aligned with the needle yoke when it's all the way up for counting bales. Brackets are available for all common balers made in the last 50 or more years, when ordering you tell us the model you have, and we make sure you get the brackets you will need. There is two wiring harnesses included one for the tractor cab and one for the baler. They feature a pair of connectors near the hitch for easy unhitching of the baler. Optional extension harnesses for rake hitches, twin baler hitches and steamers are available. The tractor harness has a power supply plug that works with the 3-blade round body amp style connectors common on most tractors made in the last 35 years. Included is a quality Ram Mount arm with U-bolt ball for mounting your monitor in any tractor on flat surfaces or round tubing.
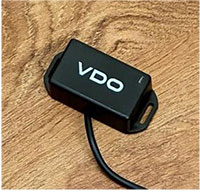
Optional GPS ground speed sensor is also available for purchase, connected to the monitor, this allows operators with older tractors and self- propelled balers know approximately how fast to go for conditions and to get back to the same speed when turning around. This is recommended for older tractors and self-propelled (mostly Freeman SP) balers that did not have a speedometer display originally.
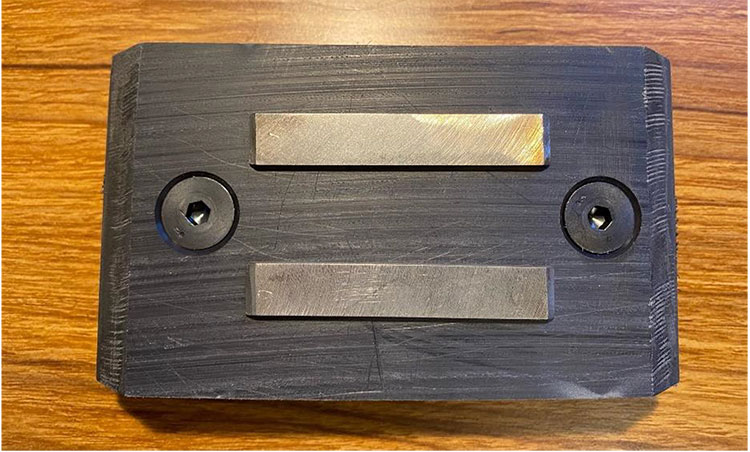
The Optional Moisture Sensor Pads are made from ½ inch thick nylon and are mounted in the chamber as close to the end of the plunger travel as possible, this way the moisture reading is more recent. They have two stainless steel strips mounted in the nylon, the strips are connected via wires to the monitor, and it measures the electrical resistance in the hay, higher the resistance the drier the hay is. It can measure 6% to 30% accurately. This is a
handy tool to know approximately what the hay moisture is and a reference to know if the conditions are changing without having to stop baling and check by hand.
You can easily install the BPM-101 yourself in about 2-3 hours from the manual that can be found on our website.
History/Origins: In 2010 Greg Hutchinson and his friend Isaac Wright took a trip to bring Isaac’s first Freeman 370 baler over 650 miles back to Ellensburg, WA from Lovelock, NV. When entering back into the Kittitas valley Isaac asked if Greg could build a flake counter for his recent purchase. Greg thought maybe he could but didn’t really see the need to since there was a company that already did that. Greg went to John Deere Tech School at Walla Walla Community College starting in 2010 and graduated in 2012, after that he worked full time at Washington Tractor in Ellensburg. While working as a field technician he saw a local farmer struggling to get his flake counter to work correctly. The existing counter relied on sensors that needed mounted magnets for it to count. It was easy for the magnet clearance to change and the counter would miscount. Greg thought there should be a way to make the counter work without magnets. From tech school Greg had a good understanding of electrical and electronics, and as he worked on more equipment, he gained more knowledge about resources and suppliers of the things needed to make his own flake counter. Late in 2013 Greg started the process to develop his first flake counter, 2014 saw the first prototype testing and first sale of what Greg called a Bale-O-Meter.
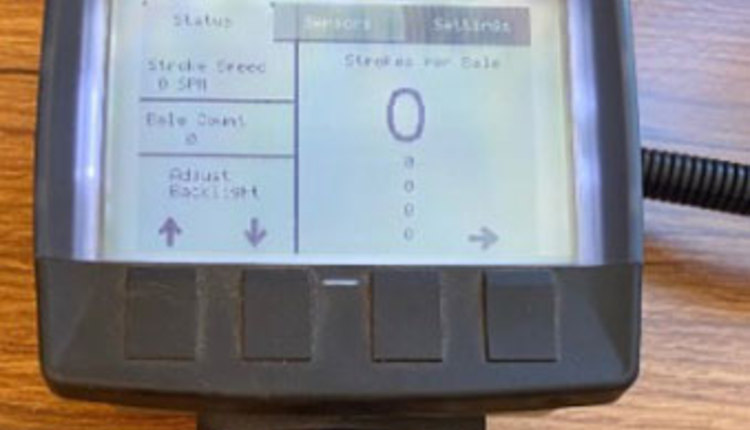
This unit went through a few software updates over the years and couldn’t read moisture but had all the same flake counter features described above. The original display was monochrome and was difficult to read in direct sunlight because of the display type and the max number size was too small. In 2019 we started development of the current model the BPM-101 which added a much better display and great direct sunlight readability. The Monitor, brackets and moisture sensor pads are made in Washington State, the wiring harnesses are made in Indiana, the Ram Mounts are made in America and the counter sensors are made in Texas, or Europe. Now over 8 years since the first one was assembled; we are selling them online worldwide. Greg has also designed hydraulic systems/controls for balers and is working on more products for balers.