The author is an extension biosystems engineering assistant professor at the University of Kentucky in Lexington.

Choosing the correct location for a hay barn can be a challenge. You might choose different locations depending on where you bale hay, how the farm is laid out, and whether you plan to sell your hay or feed your own animals. Other considerations with a hay barn site can include accessibility, drainage, and vicinity to other hay barns or livestock. Also, how the barn is oriented will influence air movement through the barn, which can influence hay quality. Ultimately choosing the right location will impact how well the barn functions.
Hay sale operations typically require a more centralized storage location for coordination of sales and loading for multiple customers. A centralized location allows one to better sort for forage quality and for customers to select the specific hay they wish to purchase.
With larger cash hay operations, a centralized storage will typically reduce the amount of equipment needed like tractors, as one tractor can service multiple barns without hauling or driving the tractors between locations. Also, one location makes it more cost effective to put in the infrastructure (utilities, drives, gates, and parking areas) for large vehicle access, and it is easier to direct customers to the location.
One challenge with centralized storage is the risk of fire spreading throughout the entire hay supply. If the hay operation includes multiple barns, it might be good to have a source of water nearby like a pond or hydrant. In addition, including a 75-foot buffer between barns will reduce the likelihood of fire jumping from one to another.
Make it convenient
When the goal of the hay operation is feeding animals, focus on getting hay as close to the winter-feeding area as possible. Typically, winter hay movement is more challenging than hay movement during the summer months, particularly if there are not good drives and access where hay is baled and stored. Inclement weather, like ice storms or extremely wet and muddy conditions, can exacerbate challenges with hauling hay in the wintertime.
The closer the hay barn is to the winter-feeding location, the better the chance that hay will be fed routinely. Moving all hay to winter-feeding areas typically provides better inventory control as well. If all the hay is accounted for near the feeding area, it is much easier to identify shortages and make adjustments earlier in the feeding season. Further, a farmer can control hay deterioration since the hay does not need to be left outside and can be more easily fed regularly in smaller quantities, which reduces waste.
In the case of feeding livestock, the focus is still on one centralized storage facility, unless the farmer has multiple winter-feeding sites. In most cases, when a hay barn is chosen for storage, a centralized storage location is the preference.
Multiple sites
If you’re baling hay on several farms and there is significant distance between the operations, consider satellite storage sites as opposed to a centralized storage. This would be very similar to grain operations that choose to have storage on multiple farms to reduce transport time during harvest.
One benefit of satellite sites is that it makes baling and hauling hay more efficient; however, the challenge is that the satellite sites may not be as secure, will be less likely to have utilities, will make coordinating hay sales more challenging, might not be in the correct location for winter feeding, and will require more infrastructure like driveways.
Without utilities present, there will not be the option of installing lights in the barn or security lights outside. This means there is more risk for someone to steal hay or equipment. On the flip side, a benefit of multiple sites is that there is some risk aversion in the case of a fire.
The proper location for a hay barn will depend on your operation and should match your objectives. Once the proper location has been selected for your operation, the next step is to decide what site makes the most sense for building the hay barn, how to build the infrastructure around the barn, and how to orient the barn for proper ventilation.
Keep water away
Since the enemy of hay is moisture, one of the biggest priorities when building a hay barn is choosing a location where water movement can be controlled. Choosing a location in a swampy area or at the bottom of a large hill will require more costly drainage infrastructure and will still be at higher risk for flooding and hay loss on the bottom hay layers. Adding gutters or rocked ditches close to barn sidewalls should be included in planning costs.
Allowing water to pool beside a barn can damage the structure as well as infiltrate into the barn and damage the hay. In addition to the outside drainage, build the barn floor at least 6 to 8 inches higher than ground level to further encourage drainage of any water that enters the barn.
Accessibility is also a priority in the planning stages. If possible, it is ideal to locate hay barns along an established drive. This reduces infrastructure costs. If you are starting with no infrastructure, budget enough to develop gravel access for tractors and other equipment to enter the barn. These gravel areas should be a few feet wider than any doors or opening on the walls of the barn and 20 to 25 feet long. Access drives are critical because the goal is to reduce mud from entering the barn. Particularly for barns with gravel bases, mud can quickly reduce the drainage capacity of the flooring and reduce the stability of the floor as well. It would be ideal to also budget for driveways and parking or turning areas. Putting down filter fabric and gravel on drives not only improves access, but it also reduces mud tracking into barns on tires and gravel loss.
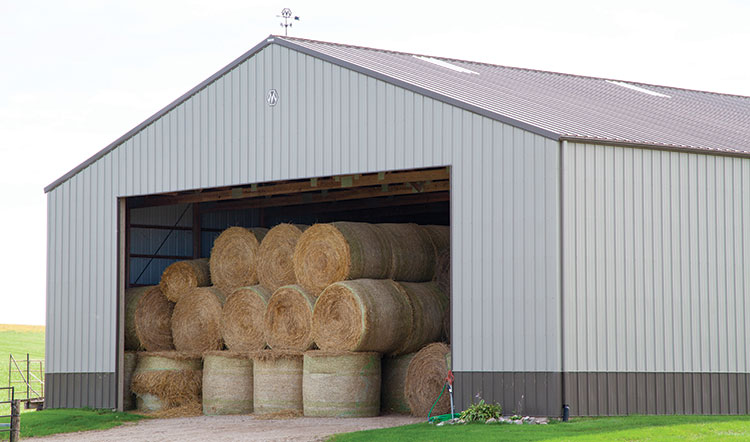
Consider air movement
A barn needs proper ventilation to expel the moisture from hay respiration. Since hay barns are typically dependent on natural ventilation to get air exchange, proper orientation can be critical. Typically, a barn should be oriented so that the sidewall, or length of the barn, is perpendicular to the predominant wind direction.
For barns with enclosed sidewalls, like pole barns, eave openings and a capped ridge vent are critical design elements to allow for passive ventilation. Air enters through the eaves and exits through the ridge vent with excess moisture from the hay. Orienting the barn so the end wall doesn’t receive the majority of weather events can also protect hay bales closest to the end wall from wind-driven precipitation.
If the barn is built as a shed style, face the open sidewall away from prevailing winds, but the side receiving the prevailing wind will still need eave openings to allow air to enter. Set up hoop barns similar to a pole barn; however, with open end walls these barns can be more forgiving to having the prevailing wind directed at the end wall.
Ultimately, a hay barn’s location is very situation specific and needs to match a farm’s operational strategies and geography. Choosing either centralized or satellite storage is a good first step in planning for permanent hay storage. Once that has been determined, the next step is selecting a specific location based on topography and accessibility. Finally, orient the barn to improve ventilation. Following these barn siting guidelines will reduce future problems and result in a faster return on your hay barn investment.
This article appeared in the November 2019 issue of Hay & Forage Grower on page 18.
Not a subscriber? Click to get the print magazine.