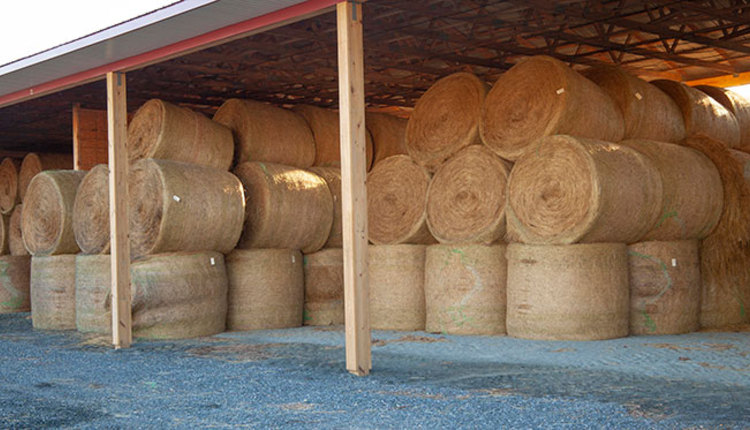
Let’s get beyond the discussion whether storing hay in a barn versus outside on the ground is a paying proposition. It is.
Instead, let’s focus on building the right hay barn for your needs. That was the message of a presentation given by Morgan Hayes, an agricultural engineer with the University of Kentucky, at the 38th Annual Kentucky Alfalfa and Stored Forage Conference in Lexington.
“A well-designed and built hay barn can be invaluable for cash hay operations,” Hayes said. “They provide an opportunity to reduce dry matter losses and maintain forage quality throughout the winter.”
Hayes explained that there are numerous styles of barns from which to choose from, the most common being a wood-frame structure with a metal roof and sides. Also popular are steel structures, with or without metal sidewalls. For round bale storage, hoop barns are a popular choice.
Hayes focused her presentation on four considerations for ensuring a constructed hay barn will be functional and effective, regardless of which barn type is selected. These considerations include: site selection, barn sizing, construction approaches, and ventilation.
Barn placement
“Site selection can make a huge difference in how effectively a barn can protect hay from weather as well as impact accessibility, safety, and security,” Hayes said. “Don’t locate your barn in a low-lying or wet area, and any excavation done prior to construction should intentionally shed water away from the barn,” she added.
A hay barn needs to be accessible for putting hay in storage and then getting that hay back out. This needs to be true in all types of weather conditions.
“Consider a large staging area and turning area for trucks and trailers,” Hayes said. “Remember, not all customers are highly proficient at maneuvering their trucks and trailers.”
The agricultural engineer also encouraged building with the future in mind. She noted that if more hay barns may someday be built, it is recommended to have 75 feet or more between barns for fire safety. She also suggested to ensure barn security by installing security lights.
Barn sizing
“The size of bales produced will influence the necessary dimensions of the barn,” Hayes noted.
As a general rule, she suggested that square bales will need a footprint of 10 to 15 square feet for every ton of hay, and for round bales, 16 to 24 square feet will be required for every ton stored.
Make the barn wide enough to allow for the hay to be stacked with a 2-foot buffer between the edge of the haystack and the wall. Similarly, allow at least 2 feet between the top of the haystack and the bottom of the trusses.
“Determine the barn capacity based on how you stack your hay,” Hayes said. “Some producers like to stack square bales the full depth of the barn, while others leave space between stacks to allow the hay to breathe better. Stacking round bales pyramid style or barrel stacking the bottom row will affect storage capacity,” she added.
One other important planning consideration is if you want to inventory hay by forage quality. This is difficult to do with only open ends and permanent sidewalls. Either constructing additional side doors or leaving one side open makes it easier to access a specific cutting or quality of hay.
Barn construction
There are a number of actual construction considerations to also be considered. First, give thought to the right flooring.
“The purpose of the barn is to reduce the breakdown of bales,” Hayes noted. “Typically, condensation on the floor is one of the most challenging management challenges in a barn. Concrete wears well with equipment loads and is easy to clean at the end of the season; however, due to its conductivity, it’s susceptible to condensation,” she added.
Pallets are often used in order to allow the floor and bales to breathe; however, they do require more labor, Hayes noted.
She suggested an elevated gravel pad for flooring as a means to preserve bottom-bale quality and also emphasized that bales not be allowed to lean against the walls in the barn.
“The sidewalls are generally not designed to handle a load,” Hayes said. “Pressure on the posts can damage the structure prematurely.”
If building an open-sided barn, Hayes reminded farmers to consider wind loads that can lift posts. She suggested to set posts at least 4 feet in the ground with a concrete anchor at the base of the post. For open-front, tall, or wide barns, place posts at least 5 feet deep.
Ventilation
Moisture accumulation during the initial storage period can be a problem with barns that are completely sealed on all sides. Also, where temperature swings occur, condensation on metal roofs and sidewalls is likely to be a problem in a fully enclosed barn.
“If barns are not well-ventilated, all this moisture will re-enter the hay bales,” Hayes said. “No-drip coatings on metal siding can reduce water dripping within a barn; however, without ventilation, the moisture does not leave the barn and can still be reabsorbed by the bales,” she noted.
Barns that are less than 70 feet long can potentially be ventilated through the open end walls. For larger barns, structures need openings at the eaves and at the bottom of the sidewalls. They also need to be vented in the roofline peak.