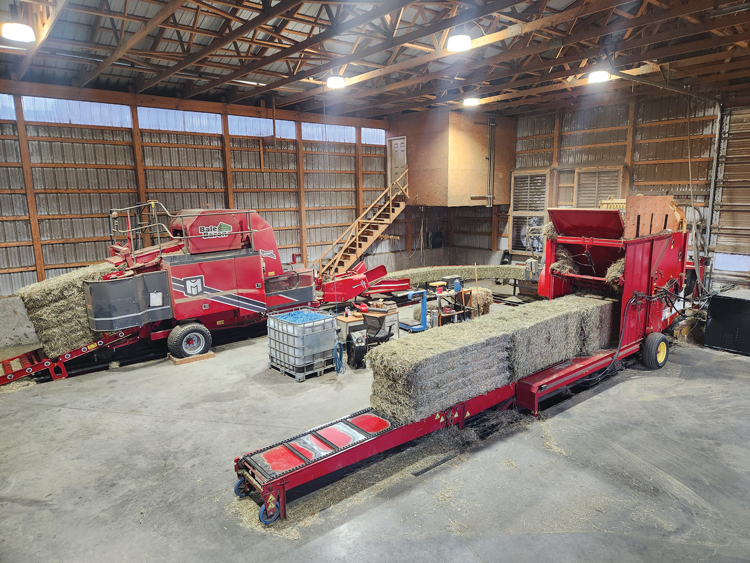
Not all teenagers have a clear image of their careers, but a young Rodney Boll knew his would look like the view of a hayfield from the seat of a tractor. The self-starter from Mount Joy, Pa., purchased his first round baler the summer after he graduated high school and has been custom baling ever since.
Boll grew up on a farm and wanted to continue working with his family, so his father suggested he buy a baler to expand the operation and make his job a more sustainable one. Lucky for him, another custom baler in the area decided to scale back shortly after Boll started his business and he was able to acquire some of those clients. His customer base quickly grew by word of mouth, and over time, he started offering other types of custom work.
Now Boll has about 100 clients. In addition to baling hay and straw, he plants and harvests forage and chops corn silage for other farmers. Planting, harvesting, chopping, and baling schedules tend to overlap throughout the summer, but rather than put all of his eggs in one basket, Boll prefers to be diversified. He takes pride in finishing every task and embraces the fast pace of custom work life.
“There is a sense of accomplishment when all of the balers come home at the end of the day and everybody was taken care of,” Boll affirmed. “Then we just have to get ready for tomorrow and we do it all over again.”
Small bales, big demand
The patchwork pattern of agricultural land in Lancaster County creates farms of many shapes and sizes, and Boll finds himself in fields that range anywhere from 1 to 100 acres. Although most jobs are relatively small, he covers an estimated 10,000 acres per season across planting, mowing, chopping, and baling.
“There are days we have 15 different jobs scattered across a 20-mile radius,” Boll said. “We will cover multiple acres multiple times a year. For example, we will mow a field in the spring, go in and merge the forage into a windrow, and then chop it,” he added.
Since buying his first round baler in 1998, Boll has added Massey Ferguson 2250 and 2270 large square balers and three Massey Ferguson 1840 small square balers to his machine shed. He also upgraded to a Massey Ferguson 4160 round baler, gained three Samasz triple mowers, and has a Claas Jaguar 870 chopper. His equipment line-up allows him to meet a variety of customer needs, which ultimately revolve around their target markets.
Horse owners tend to buy small square bales since they are easier to handle than large ones, and there is also a demand for straw in and around construction sites for erosion control. With that said, small bales represent a large portion of Boll’s production; however, making and handling them can take up a large portion of his time. One way he overcomes this is by running two Marcrest Bale Barons, which make hay easier to collect and transport.
“When we small bale, we drop the bales on the ground and come through with the Bale Barons, which pick up the bales and package them into bundles of 21 that are essentially like a large square bale,” Boll explained.
From large to small
The Bale Barons enhance efficiency to an extent, but making small bales is still rather tedious. Baling large bales, on the other hand, requires much less time to cover the same area of ground. About 10 years ago, Boll and his father began brainstorming ways to build a machine that could convert large square bales into small ones. Much to their surprise, such a contraption already existed.
“With small square balers, it takes four or five machines to do the same number of acres per hour as one large baler. It takes a lot more labor to be small baling in the field, and you are limited on how much you can do. We couldn’t do enough,” Boll said. “Then we stumbled across the Bale Converter, and with that we could harvest hay quickly with a large square baler, get it under cover, and then convert it to small square bales when we had time.”
The Bale Converter ultimately tears up large square bales so hay can be reconstructed into small bales. It was a game changer for Boll before a barn fire destroyed his machine in 2018. Despite the disaster, Boll went straight to the drawing board to make a blueprint for a new barn. The crafty custom baler designed a building for hay and straw storage that also had space for an integrated bale conversion system.
Boll bought another Bale Converter and put it on one end of the new barn where it sits at the right-hand side of the U-shaped conversion system. Large square bales are untied and pushed into the machine, and after the Bale Converter shreds the bales, the hay is fed directly into a Massey Ferguson 1840 baler. Hay is then reassembled into small square bales before it moves along a curved chute that is connected to a Bale Baron on the left-hand side of the conversion system that compresses them into packs of 21.
The task takes about five to eight minutes from start to finish — depending on forage species — which means Boll can rebale almost 300 small bales per hour. The Bale Converter, the baler, and the Bale Baron are all powered by electric motors.
“We knew what was working and we knew what we wanted, so we made this makeshift system,” Boll said. “What the Bale Converter does is mimic a windrow in the field by tearing apart the hay and feeding it to the baler. It’s a unique thing that serves the niche market we have.”
Any hay that is lost in the process is collected by three in-floor augers that run under each leg of the conversion system. These augers, which are covered by steel crates for safety reasons, lead to a vertical auger that delivers chaff to the front of the baler, virtually eliminating waste.
Helping hands
The conversion system runs almost every day, and operating it is a full-time job. Boll converts many of the bales he makes for his customers, but he also converts bales for farmers who harvest their own hay. At least two of his nine full-time employees always stay back at the barn to feed the Bale Converter and move bales while the rest of the crew is in the field.
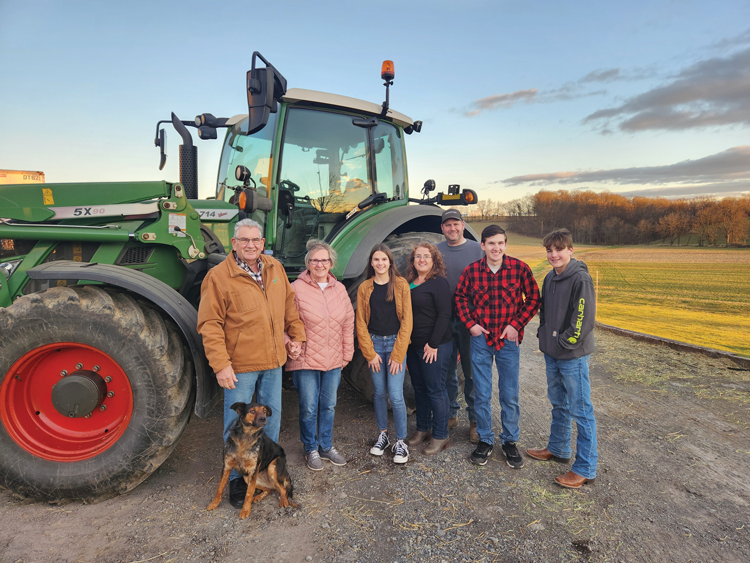
“People bring their product to us and hire us to convert it. We rebale far more than what we bale on our own,” Boll stated. “Some have their own trucks, and we do trucking for those who don’t. Either way, there are trucks coming every day.”
In addition to working in the field, converting bales in the barn, and trucking hay on the road, Boll appreciates his employees’ assistance with maintaining and repairing equipment in the shop. He typically trades in his small square balers every year but decided to keep his large square balers and round baler in 2023 given high equipment prices. He was confident these machines were still in good condition going into the fall, and with a handy team and a reliable equipment dealer, breakdowns aren’t too concerning.
“We have a really good group of employees who make my job a lot easier. I’m grateful for all they do for us,” Boll said. “We do daily maintenance ourselves, but I will have my dealer service the balers every winter. They go over things with a fine-toothed comb and replace whatever they think is necessary. And if we do have a breakdown, he can usually get to us within a day, and often within a few hours.”
Among the team is his father, Jay; his wife, Heather, who manages bookwork; and his oldest son, Landon, who recently graduated from high school. Like Boll, Landon is eager to stay involved in the custom operation business and hopes to have a career in agriculture of his own. It was this resolve that led Boll to start baling years ago, and it will likely be what carries the custom operation into the next generation that also includes son Kadon and daughter Dori.
This article appeared in the February 2024 issue of Hay & Forage Grower on pages 6-7.
Not a subscriber? Click to get the print magazine.