Aside from the bale size being made, there are many differences among round balers and selection of a machine that best matches your needs is key.
The first important question is, “Do you intend to use the machine for dry hay or baleage (or both)?” Interest in baleage is rapidly expanding as a method to harvest and store high-quality forage on beef and dairy farms.
However, it is important to remember that a bale of baleage weighs three to four times as much as a bale of hay, straw, or cornstalks of the same size. The heavier duty silage balers are better able to handle baleage without breakdowns and will generally produce better bales.
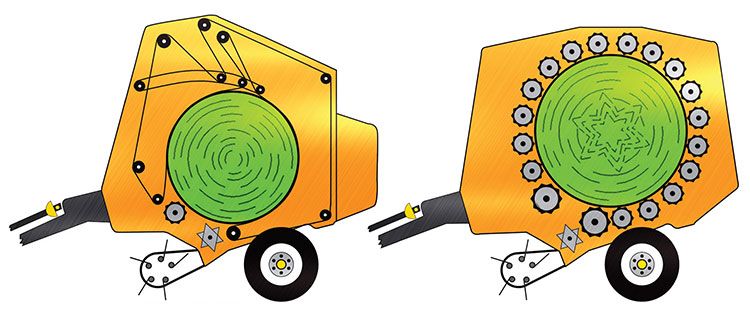
Variable or fixed chamber?
The second consideration is fixed versus variable chamber balers. The variable chamber baler has been the most common in the U.S. The belts will make bales of more consistent density throughout the bale and of greater density (important for baleage) than a fixed chamber baler.
Fixed chamber balers are mechanically simpler, as they don’t need the mechanism that varies the chamber size as the bale grows. These balers will make bales that have less dense centers. Some have claimed that this is good for drying hay; however, research has shown no drying advantage to hay bales made at 16 to 18 percent moisture with low-density centers. Hay bales with less dense centers may be advantageous when feeding smaller animals that have less trouble tearing the lower density center of the bale apart when eating at a feeder.
Until recently, most variable balers would not bale in wet forage conditions due to gumming on the belts. This was less of a problem for fixed chamber balers. Newer variable chamber balers have designs to reduce the gumming issue on belts and bale chamber-forming rolls in wet conditions.
Tractor ground speed must be lower for fixed chamber balers or bales will be less dense. One option is to drive faster initially and then slow down to 4 to 5 miles per hour (mph) for the outer bale shell. This drawback is more prominent with economy fixed chamber balers than high-end balers.
Fixed chamber balers tend to be noisier than variable chambers due to the bale chamber chain operating on idlers.
The other consideration is that most fixed chamber balers (except a few high-end models) can only make one bale size. This is fine for making baleage, but smaller bales are sometimes desired when making dry hay, especially if baling a little wet and wanting to minimize bale heating (smaller bales at 16 to 18 percent moisture heat less than bigger bales). A fixed chamber baler is also a disadvantage at the end of the field with a part bale in the baler where you have a clump of hay rather than a small bale.
Netwrap rules
Most round baler manufacturers are moving away from twine to the use of netwrap or, more recently, solid plastic wrap. Wrapping is faster with plastic than twine. Furthermore, netwrap or solid plastic-wrapped bales have reduced leaf loss when handling. There is also less rain uptake if bales are left outside. However, plastic should be removed before feeding to animals, especially with bale feeding machines, since plastic remaining in the hay is consumed by animals and may cause health issues.
Another consideration when selecting among balers is the number of bars on the pickup head. Economy models come with four bars while better machines have five. The five-bar designs tend to leave less hay in the field and have reduced leaf loss during pickup.
Consider purchasing a round baler equipped with a precutter. Cutting the hay or haylage into 4-inch lengths before baling has been shown to reduce feeding loss. This is because an animal is able to swallow most of a bite and not have to chew and drop lengths of the forage onto the ground. The reduced length of precut hay or haylage has been shown to boost forage intake and improve animal gain. Modest bale density gains might also occur. The recommendation is to precut to a 4-inch length, which most balers can achieve by removing some knives.
Recent innovations
An option that may be advantageous, especially if making many alfalfa bales, is a bale accumulator. Forage starts to regrow as soon as it is cut. If taking a few days to dry, baling hay and bale removal drives down regrowth and reduces the yield of the next cutting.
A bale accumulator will collect bales and drop them in rows or at the end of a field to reduce the amount of driving across the field needed to remove the hay bales. Always plan on removing bales from the field as quickly after baling as possible.
One of the newest innovations for round balers is the introduction of bale wrappers. These balers will produce baleage wrapped in plastic ready for storage.
Some of these balers eliminate the need to stop the baler for the wrapping process. These machines are much larger and costlier and are designed for farms or contract harvesters who harvest thousands of bales annually.
Match baler with tractor
When purchasing a baler, consider the size and power of the tractor. The tractor horsepower needed for baling will depend on baler size, whether fields are level or sloped, desired baling speed, whether hay or baleage is being made, and if a bale accumulator is part of the package. Consider your tractor size and the front axle and tire weight capacity for transporting bales, especially if you’re planning on carrying more than one bale on a front-end loader.
Round balers are important tools for making quality hay. It is vital to consider these discussed factors when purchasing a baler that will meet a farm’s individual needs.
Lastly, here are a couple of management tips when making round bales:
- It is always best to have a windrow as wide as the width of the baler pickup head for making uniform diameter bales.
- Make baleage or bale hay when forage is slightly tough to minimize leaf loss with variable chamber round balers.
This article appeared in the January 2019 issue of Hay & Forage Grower on pages 20 and 21.
Not a subscriber? Click to get the print magazine.