This item has been supplied by a forage marketer and has not been edited, verified or endorsed by Hay & Forage Grower.
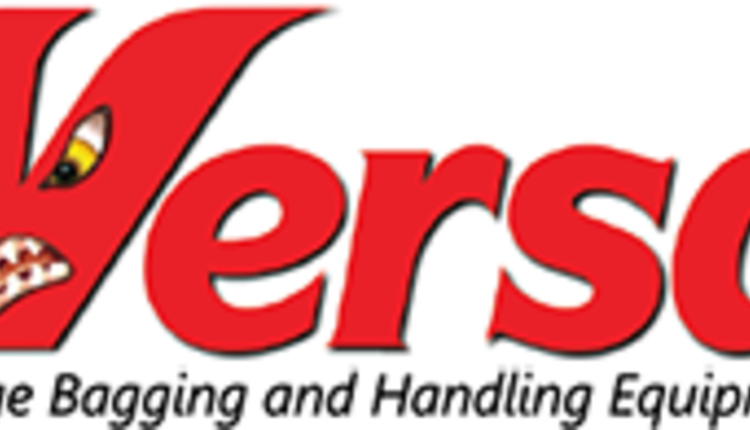
For bagged silage specifically, expert forage consultants, in the dairy and cattle industry, see benefits to this approach but are united that results can only be maximized through well executed feed management – specifically the proper placement and packing of the bags.
“It’s all about good feed management. [When packed correctly] bagged silage can have a huge impact on profitability, herd health, and milk production,” says Bonni Kowalke, fermentation researcher, practitioner and owner of Stem Ag Consulting, LLC., a firm that specializes in monitoring and optimizing dairy farm inputs and outputs at all forage production stages.
To help dairy farmers optimize their operations, several consultants and an equipment supplier offer tips on how to properly pack bags, as well as feed management tips to obtain the highest nutrient density silage.
Optimal Silage Packing = Less Spoilage, More Nutrients
For many years, Kowalke has maintained her favorite storage system is a bag.
“The reason I say I love bags is it is the only one storage system that – if packed properly – is a completely sealed vessel,” says Kowalke, adding that is not necessarily the case with bunks, piles, or upright silos.
She adds that insufficient packing, which fails to minimize oxygen exposure, can result in spoilage of ensiled forage, and lead to feed loss.
“With a bag, you have more control over the spoilage if done properly. It is critical for cow health, milk production, components, and profitability to avoid feeding spoiled silage because of all the negative consequences,” says Kowalke.
According to the University of Delaware research study “Effects of incorporating spoiling corn silage into a total mixed ration for dairy cows” (Steele, L. C., Moyer, K., Hellings, E., and Kung, L. Jr. 2018), even a relatively small quantity of spoiled silage in a Total Mix Ration (TMR) can decrease dry matter intake and digestibility.
“Many people think that you have to put a lot of spoiled silage into a TMR to get a cow to back off, but that is not the case,” says Kowalke. “The cow may ingest it, but it is not going to be as digestible.”
Dr. Keith A. Bryan, Technical Service Manager Silage and Dairy, North America, for global biosolutions company Novonesis, agrees. Dr Bryan, who holds a PhD in Animal Science, sums up his company’s approach as advocating for good feed management practices in combination with effective silage inoculants.
“In terms of silage quality at feed out, the number one limiting factor is packing density, specifically suboptimal packing density in a bag,” says Dr. Bryan.
Proper packing of the silage can maximize the nutrient value of feed.
“Minimizing yeast and mold allows us to preserve more nutrients in the silage. The feed is more nutritious because we are not losing nutrients to those spoilage microorganisms, and we are not introducing contaminants into an animal that we are asking to grow rapidly and efficiently or make large volumes of milk,” says Dr. Bryan.
Efficiently producing and packing high quality silage also reduces the cost of feeding and maintaining dairy herds.
“Animals eat to meet their energy and nutrient needs,” explains Dr. Bryan. “So, if [the silage] is suboptimal and retains only 90% of its full nutrient density during the ensiling process, then we have to feed it 110% [of the silage] to get the same total nutrients into the animal.”
The Advantages of Bagged Silage
The effective use of silage bagging can provide several advantages to dairy farms, including more controlled feedout to maximize nutrient availability and minimize spoilage and loss.
“With the large bags the feedout face is so much smaller and you go through a bag so much quicker than a huge drive over pile or bunker,” says Dr. Bryan.
“So, if packed correctly and by feeding it out more quickly, oxygen penetration is reduced and you can have more hygienic feed in terms of reducing yeast and molds…compared to a bunker or a pile,” he adds.
Steve Massie, Head of Nutrition at Renaissance Nutrition Inc also considers the small face at feedout a key advantage to bagging.
“When bunkers become too wide or high, feeders may only use from a third to half a face and it can take 48-72 hours before they get back to the silage,” says Massie. “By that time, air has gotten into that face, which can result in yeast and even mold growth if spores are present, particularly in warmer conditions.”
He adds that very good feed managers will set up the feeding face of a bag so only 6-11 feet is used daily to keep [the rest of] the silage fresh.
Massie points to another advantage: the ability to select the best, higher quality forage. He explains that most dairy farms have silage that is a little fresher at a given time, a factor that can spur milk production. With a bunker, “you start at one end and feed your way through; whatever is there, that is what the cows get,” says Massie.
As an international dairy consultant, Massie says he takes forage samples, matches those with the farm's goals and current production levels, and creates a tailored grain mix for the farms.
“We sample all the silage in the bags so we can feed the best forage to the cows year-round and potentially help make the dairy the most money,” says Massie.
Placing various crops and cuttings into separate bags offers dairy farmers the flexibility to create silage and mixed rations tailored to their specific needs and even the cow’s stage of development.
This approach can be particularly beneficial with specialty crops. Depending on the dairy operation, Dr. Bryan may recommend putting up a variety of feeds into bags because that provides maximal flexibility in storage and feedout of different crops at different times of the year or to different physiological stages of animals within the dairy.
Achieving Optimal Packing Density with Baggers
To maximize the effectiveness of their equipment, dairy farmers should prioritize packing pressure as a key factor to consider for equipment selection. With proper internal density, the oxygen is removed almost instantly, and fermentation begins promptly. The sealed bags protect silage quality and maintain favorable fermentation conditions even amid unfavorable conditions such as exposure to rain, moisture, excessive dryness, or prolonged storage.
While Renaissance Nutrition’s consultants like Massie do not recommend specific types of baggers, they do suggest some desired features on bagging machines.
“Many [dairy] farms don't understand the stretch bar on a silage bag. They need to stretch the bag to maximize the tonnage going in as well as keep it packed very tight to squeeze out the air. If you under-pack it, you get more trapped air which can really cause some issues,” says Massie.
He also has suggested that they, “extend the tunnel to let the feed push against steel instead of just air to get a better, tighter bag and take the lumps out.”
Fortunately, as silage bagging has increased in popularity with dairy farms over the years, the equipment has continued to improve. Today, the process of creating bagged silage for dairy farmers is relatively simple. Essentially, side unloading wagons pull up alongside the bagger and unload onto the bagger conveyor. End-dump wagons or trucks back into larger table load baggers to unload and start bagging. Capacities generally range from 2-5 tons per minute for side unloading wagons to higher capacity truck rear-end loading models that handle from 4-16 tons of bagged silage per minute.
To maximize the effectiveness of the equipment, however, dairy farmers need to clearly understand the key factors that affect bagging machine efficiency and capacity. At the top of the list is packing pressure, according to Steve Cullen, President, Astoria, OR-based Versa Corporation, a global leader in agricultural silage bagging and handling.
“It is important to have a good balance between the pressure caused by the packing rotors and the braking of the bagging machine. The goal is to firmly pack the bag without over-stretching the bag while gradually moving the machine forward as the bag fills,” says Cullen.
Among silage bagging equipment, packing is approached in various ways. Some systems utilize a cable system with a heavy net backstop, a concept first introduced in North America in 1976. After each bag is filled, the cables must be rewound, and the backstop moved to the next location.
To eliminate the need for external cables, Versa created an innovative cable loop Internal Density System® that uses a single adjustable cable inside the bag. The OEM also developed a heavy-duty belt Internal Density System® that slides under the bag and pulls it tight lengthwise. This facilitates tighter packing of longer silage bags than the industry norm. The largest models, such as Versa’s high-capacity ID1014 bagger, can be used to bag up to 14-foot diameter bags that are 500 feet long.
Expert Tips for Bag Packing
With a wide range of silage bagging technology currently on the market, experts provide some advice on how to determine if their bag is packed correctly.
Watch for Bag “Puff Up”
According to Kowalke if the bag is filled quickly and sealed completely, the bags should “puff up” in a few days due to the fermentation gases. She recommends having a vent at the top of the bag, or oxygen barrier, to release the oxygen. After a few days of fermentation, the vent should be closed and the bag completely re-sealed.
“[the silage] is going to be perfect. That's why I like bags,” says Kowalke.
Take Your Time
When silage bagging, Kowalke advises that there is no need to rush the packing process with an overpowered tractor. Smooth, packing is more important than speed to retain consistency.
“You don’t need to pack that fast. Take your time. You often have to wait for the next truck anyway. The packed bag shouldn’t look like a camel’s back, which can happen if you rush with a high-power tractor,” says Kowalke.
Control the Environment Around Bags
Whether piles, bunkers, or bags, controlling the surrounding environment is important to avoid animal intrusion.
“With all of those [storage] systems, the biggest enemy of our forage quality is air getting in there and moisture or precipitation, water, rain,” says Kowalke.
This means eliminating tall grass and standing water, which can provide shelter to birds and rodents.
Although many dairy farmers are at least relatively familiar with bagged silage, those who become informed about which key qualities to consider before purchasing equipment will maximize the health, productivity, and profitability of their herds.
For more information, call (800) 837-7288 or visit versacorporation.com.