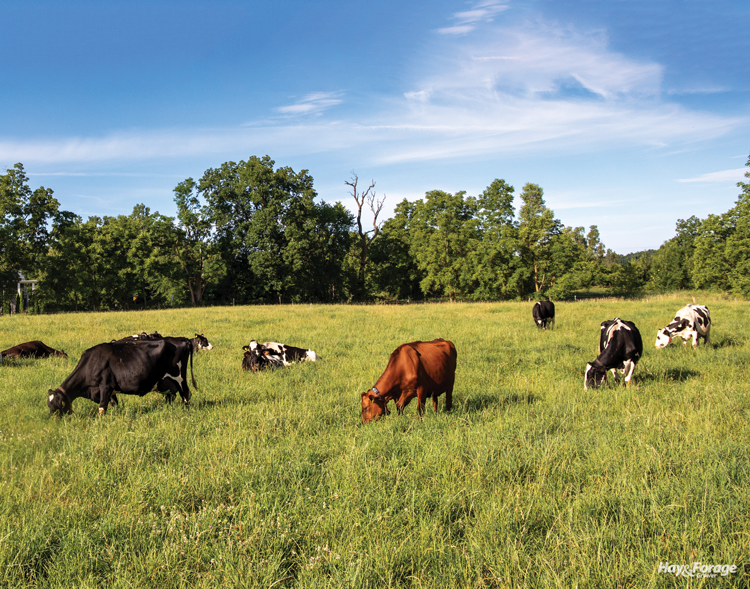
What happens when a Michigander meets an Irishman . . . in New Zealand? At least in one case, and there may only be one, a unique grazing dairy called Annie G’s springs up just outside of a city better known for wolverines than cows.
Kat (Lambarth) Mageean grew up on a farm originally purchased by her great-grandfather in 1924. Her father operated a conventional dairy, building both a milking parlor and freestall barn in the early 1970s. Kat went off to college, became a veterinarian, and eventually found herself practicing veterinary medicine in New Zealand. On an arranged date, she met Dave Mageean, who was from Ireland and working in the island country on a custom silage crew while also trying to break into the artificial insemination business. A year later, the two were married and moved back to Kat’s family farm near Ann Arbor, Mich.
Dave and Kat bought the dairy herd from her parents and slowly started to buy the land. In 2017, the couple’s experiences in New Zealand and Ireland prompted them to convert the conventional dairy into a grazing operation. “My dad and neighbors thought we were nuts, but we had a lot of good statewide mentors and our own experiences to fall back on,” Kat related during a visit to their farm last summer.
In addition to a goal of grazing their herd, Dave and Kat also wanted to milk with robots, so they built a new freestall barn equipped with two automated milking systems that sits near, but not on, the original farmstead. This was a labor-saving decision as Kat was still working off-farm as a veterinarian.
A blank slate
Although the couple had learned a lot from their overseas experiences, they are quick to acknowledge that the climate in Michigan is different, and you can’t just take a New Zealand system and model it here. Still, having come from a background where grazing, pasture rotations, lanes, and fencing comprised the normal mode of operation, there wasn’t a steep learning curve for Dave from those perspectives during the farm’s makeover.
“It was nice in the beginning because I was starting with a blank slate from the standpoint of how I wanted to set up the lanes and paddocks,” Dave said in his still present Irish articulation. “But I still lost a lot of nights’ sleep thinking about how I wanted to construct lanes so that the cows could get back to the barn to visit the robot at any time, but yet I could still move machinery down lanes if I had to. Essentially, I set it up in blocks, so if the cows were in one block, I could operate in a different block without disturbing their grazing or trips to and from the barn,” added the amiable dairy farmer.
“There were things we did intentionally that worked out, but there were also things we did unintentionally that worked out,” Kat related. “All in all, we’re really happy with the set-up we have now.”
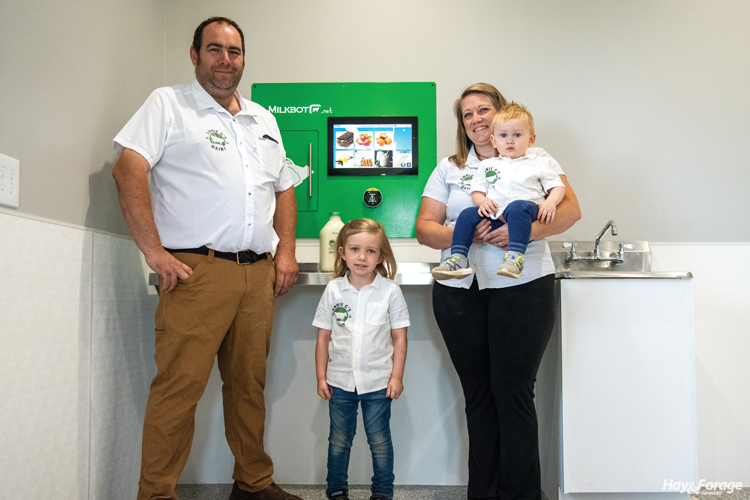
Thinking back, Dave noted they did make one big mistake when converting to a grazing system. “We seeded all the pastures down to alfalfa and timothy. It was the recommendation of my nutritionist at the time, and it was a disaster. To mitigate that situation, we killed the alfalfa after the first year and seeded a pasture mix along with additional perennial ryegrass and red clover.”
In the pasture-robot milking system, the 85-cow, mostly Holstein herd isn’t “fetched” for milking; they come into the barn and go back out on their own. The cows are given new grass every 12 hours at 5 a.m. and 5 p.m.; however, with each switch to one of the 28 paddocks on the farm, they will be guided in a different direction from the milking barn by the automated gate system. Often, paddocks are split in half with polywire. “We can do a 21-day rotation quite easily,” Dave noted. “Heifers often graze behind the cows in a leader-follower system and calves, which are raised under the watchful eye of Kat, are put out on pasture once they are 5 to 6 months old.”
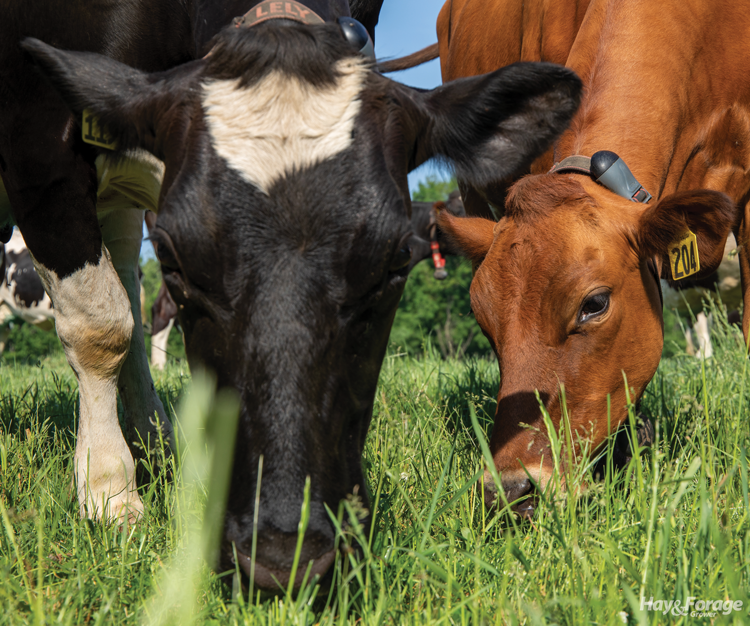
When the cows are on pasture, they average about 2.5 milkings per day. That average moves up to 3.8 milkings per day when the cows stay in the barn during the winter. “The lure of new grass is the driver that gets cows back to the barn to milk,” Dave explained. “Some of them will try to get back out before getting milked, but the automated gate doesn’t let that happen. You’d be amazed at how fast the cows learn the system,” he added.
These days, Mageean interseeds about 20 acres of pasture every year in March with a mixture of ryegrass, clover, and tall fescue, using a 10-foot Lilliston no-till drill. This past year, he tried a 10-species mix of cool-season grasses, legumes, and forbs on a couple of paddocks to see if he could improve season-long production.
“I like to clip all of our pastures by June 1, usually after the second rotation through,” Dave noted. “Once grasses head out, they are not going to be eaten, and I don’t want to see those brown, poor-quality plants standing out there all summer.”
Need for winter feed
Being in Michigan, the Mageeans still have a fairly long nongrazing season that requires the need for stored feed. “Our grazing season begins in mid-April and ends about mid-October, although the heifers may stay out a little longer,” Dave said.
In addition to his pastureland, Mageean also has 60 acres of dedicated hay ground that is harvested either as baleage or dry hay four to six times per year. Baleage fields consist of alfalfa, ryegrass, and red clover while the dry hay comes from fields seeded with soft-leaf tall fescue, late-maturing orchardgrass, and a little timothy. He also grows 60 acres of corn for silage that is stored in a bunker silo and helps keep cows fed during the winter. From time to time, he also grows some cereal grains that are harvested as forage. During the nongrazing months, cows are fed a total mixed ration.
Hay and baleage quality are critical to Mageean. “I’m one of the first ones to cut in the spring, and I always cut based on grass maturity. After that, I gauge my cutting time based on the alfalfa. Everything gets cut at a 4-inch height. When making baleage, I try to have bales wrapped and stacked within an hour and a half of baling.”
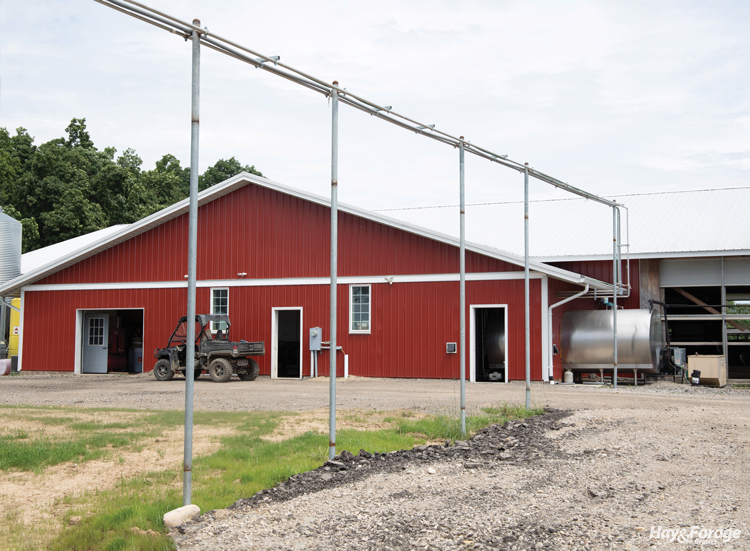
The next steps
With the grazing-robot milking system pretty well perfected, the Mageeans, who are now also raising two young children, Annie and Angus, are moving on to the next step in their long-term plan. “We always knew that we would need some sort of niche market to milk 100 cows and survive, even though I worked off the farm as a veterinarian,” Kat shared. “We wanted to sell product direct to the consumer.”
The Mageeans recently built a Grade A milk processing facility near their current barn that is equipped with a pasteurizer and self-serve milk vending machine (milkbot.net). Beginning last summer, the general public can stop and fill the provided bottles with milk from the farm’s totally A2 milk-bred herd. It’s the first such vending machine in the U.S., although several are in operation in Europe. Different flavors of the nonhomogenized milk are also offered.
“We built the facility big enough so that we can expand to making more products in the future,” Dave said. “Kat does all of the required milk testing and has developed a marketing plan. We are really excited about this new venture.” Based on their Facebook page (Annie G’s Dairy), so are their customers.
This article appeared in the March 2025 issue of Hay & Forage Grower on pages 6-8.
Not a subscriber?Click to get the print magazine.