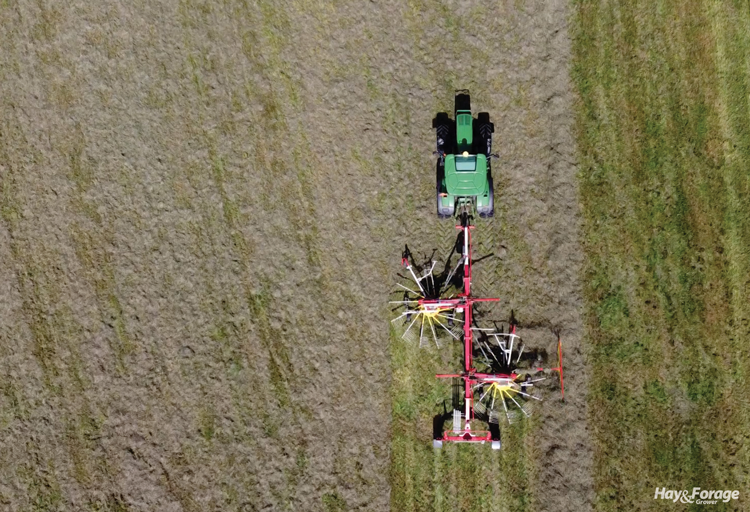
The Northeast Kingdom of Vermont stands out from the rest of the state in more ways than one. Geographically, it comprises three counties wedged between the Connecticut River and the Canada border. Visually, it is home to some of Vermont’s most scenic drives, panoramic views, picturesque hikes, and pristine waters.
Notably, the National Geographic Society once named the Northeast Kingdom the most desirable place to visit in the country. Economically, it may not be the most desirable place to operate a grass-fed dairy, but Andy and Mateo Kehler figured out a way to do so successfully.
In 1998, the brothers bought land near the town of Greensboro that would later become Jasper Hill Farm. At the time, several small-scale dairies in the area were struggling to sell enough milk to make a profit. Andy and Mateo — whose love for the land was matched only by the love of their 50-cow herd — were seeking a solution to improve razor-thin margins for themselves and their neighbors.
The Kehlers built a creamery and set out to use their cow’s milk to make European-style cheeses that boasted the highest prices on the market. They started selling cheese to a few shops and restaurants, but their customer base quickly grew along with the recognition of their award-winning products. To keep up with demand while expanding cheese selection, the brothers also installed a seven-vault underground aging facility beneath one of their pastures.
Today, Jasper Hill milks about 200 cows and buys milk from five nearby dairies. Those partner farms receive a premium for their product that they wouldn’t otherwise see if their milk was sold as a commodity. Jasper Hill also has over 80 local employees working in their parlors, the creamery, cheese cellars, and crop fields. It’s what the Kehler brothers always intended for their business model — to support small dairies and keep area agriculture a lucrative opportunity.
Forage is king
Jasper Hill encompasses about 1,000 owned and rented acres that are all used for pasture and hayfields. They don’t grow any corn or other annual species.
In addition to working on the food safety team in the cheese cellars, Maddie Calderwood oversees pasture management at the dairy. Her husband, Andy, is a part of the cropping team. Cows can typically graze from mid-May to mid-October, but in the offseason, hay is the primary component of their rations since the milking herd does not eat any ensiled feed.
Calderwood explained that silage microbes can be problematic for their creamery. Certain associated bacteria can ruin the texture and flavor of the cheese and may include pathogens. What’s more is fermented feeds compromise the farm’s goal to accentuate its “taste of place” by reflecting the profile of their local forages in the flavor profiles of their products.
“The complexity of the milk that we are making is preserved in the cheese,” Calderwood stated. “Whatever is in the milk gets amplified in the cheese process. That means our farm is managed quite differently than a normal dairy.”
All hail the hay dryer
An emphasis on dry hay requires ample investments to combat the humid climate. One of the greatest investments at Jasper Hill is the 11,000-square-foot hay dryer located on their storage site, which is called the Randi Albert Calderwood Cropping Center in honor of Calderwood’s late father-in-law.
In tandem with its European cheesemaking techniques, the farm drew inspiration from a hay drying approach in the Emilia-Romagna region of Italy, which is famous for Parmigiano Reggiano, or Parmesan, cheese. They worked with AgriCompact Technologies to design a hay dryer like the ones found on those Italian dairies and installed the first machine of its kind in the United States in 2015.
The facility was originally built to dry round bales, with two drying chambers on either side of the dryer. Each chamber had an array of 50, 5-foot circular vents carved out of the cement floor where individual bales were placed face-up for drying. But when the cropping team invested in a large square baler in 2023, the chambers had to be modified.
By retrofitting a grid of rectangular vents, the hay dryer’s total capacity doubled from 100 round bales to 200 large square ones. The crew uses a telehandler to place a single layer of bales on the floor of either chamber, sliding the doors shut to begin the drying process. For the dryer to function, though, the chamber must be completely full.
“The idea is that the bales create a seal over the vent spaces so the forced air has an equal effect on each bale, pushing moisture out of the bales from the bottom, up, and out the top,” said Ellie Searles, another member of the cropping team. “The moisture is evacuated from the chamber through a window of louvers, and we control whether the hot air that has passed through the bales is recycled back into the system or expelled.”
The dryer can operate with hay from 25% to 35% moisture. Although the duration of the drying process depends on the initial dry matter of the bales, it generally takes 72 to 96 hours to go from 25% to 10% moisture. That time frame was one trade-off of doubling the capacity of the dryer when the team reconstructed it to accommodate large square bales.
“Increasing the capacity of the dryer floors extended our drying time because now we are drying twice the volume of feed,” Searles said.
Since there is only a short window of time to ted hay and begin baling after the morning dew dissipates in this part of the Green Mountain State, the dryer essentially brings damp hay down the homestretch. Even on the sunniest of summer days, ambient moisture can run up the relative humidity so that the rate of drying is dismal at best.
“It’s really deceptive that the hottest days are also so humid that the hay does not get all the way dry,” Calderwood said. “Our hay dryer is an extra tool to get hay that is the quality that we need.”
A bit of baleage
Given that its moisture threshold tops out at 35%, the hay dryer isn’t always a viable tool. The cropping team reserves baleage as a last resort if wet forage needs to be baled immediately. Sometimes, fresh-cut hay must be moved off the field ahead of a string of showers. Other times, it gets rained on unexpectedly. At Jasper Hill, this fermented feed is only fed to dry cows and heifers.
“Plan A is getting hay baled at the right moisture right away. If we can’t do that, we will put it in the dryer. And if that won’t work, making baleage is our backup to make sure hay doesn’t go to waste,” Calderwood stated.
Everyday hay decisions and last-minute baleage calls are ultimately made by the farm’s manager, Nate Hunnewell. “It’s a team effort, but Nate is in charge of the farm, and everyone is usually on the same page,” Calderwood explained. “Everyone knows what field needs to be mowed next, and people generally do the same things: Ellie mows, Gary teds, Andy rakes, and Norm bales.”
All dry hay is sampled and organized according to forage test results, and the farm works with a nutritionist to determine different rations for high-producing cows, less competitive milkers, and those later in lactation.
“Because we are feeding dry hay, our milk production is lower than that of a farm that is able to feed a lot of corn silage and haylage,” Calderwood said. “Having the highest quality possible is really important for hay.”
Grazing gleanings
Forage quality is also important in pastures. Orchardgrass dominates the decades-old mixed stands, which also include various types of clover, plantain, and vetch. Reed canarygrass is prevalent in low-lying areas and poor-drainage soils, although it is less-than-desirable by Calderwood’s standards.
“I don’t like reed canarygrass,” she asserted. “It’s pretty unpalatable for cows, and it indicates really wet pastures, which are a trouble to manage. We don’t like the cows to be in a wet pasture for long because they tend to punch it up.”
The lactating herd is turned out to grass after each twice-a-day milking. Calderwood estimates an appropriate paddock size and then monitors plant height and animal behavior to maximize forage utilization and determine rotation patterns.
“The cows are not on a set grazing schedule — we just take a stab at how much we think they will eat and watch plant residual until it looks like it’s time to move them,” she explained. “My best indication is that if the cows could not care less to see me, they have plenty of feed.
“If they see me, become alert, and are willing to follow me, it’s time to go to the next pasture,” Calderwood continued. “If they see me and they start mooing and chasing me, then I know they didn’t have enough to eat.”
The biology major started working on dairies after college when her studies spurred an interest in grazing ecology. Since then, she has lived on farms in the Northeast, Missouri, and as far away as New Zealand, knitting together the knowledge she has gleaned at each location.
“The learning curve was great for me. After college, I felt like I had my head in books for so long that to work on a farm I had to start from zero,” Calderwood shared. “We bounced around to a handful of farms and got to work with a lot of different people, and each person did a few things really well.”
One thing she wants to improve upon in the grazing acres at Jasper Hill is the proportion of clover in pastures and hayfields. Not only would more clover reduce the amount of fertilizer needed to boost grass production in either system, but the natural reseeding of these species should indicate optimal soil pH and healthy soil conditions.
“Especially in our hayfields, we are really trying to encourage more clover over time because it’s an indication that we are doing the right thing,” Calderwood said. “We are trying to minimize our conventional fertilizers as much as we can. We do still use some, but again, there’s a balance between the cost of fertilizer and what we are getting off the field.”
Crown jewel components
Healthy soil and healthy forage translate to healthy cattle. The 200-head milking herd comprises a mix of Holsteins, Jerseys, and Brown Swiss cows to ensure adequate milk volume, fat, and protein for making cheese.
“Holsteins can produce an insane amount of milk, but it might not be exactly what we want for our cheese,” Calderwood said. “Our Holsteins add to the tank, but those other breeds are higher in components.”
Higher components are key for the specific fatty acid profile and fat-to-protein ratio the farm has resolved to achieve. Despite a cow’s innate ability to turn fiber into fat and protein, though, the farmers know high-quality milk is derived from high-quality feed.
“It takes a lot of money to make this hay, and this is not the cheapest way we could do it.” Calderwood asserted. “Our company is kind of going along the path of most resistance.”
Traversing this path requires a lot of problem solving and troubleshooting. “I don’t think anyone wakes up in the morning and knows exactly how the day is going to go — we never do the same thing. It’s complicated, but it’s fun, especially when you get things right,” she beamed.
Even so, it’s safe to say that hay and forage reign supreme at Jasper Hill Farm, and their efforts to capture the “taste of place” of the Northeast Kingdom come full circle in the shape of a wheel of aged cheese.
This article appeared in the April/May 2025 issue of Hay & Forage Grower on page 6-8.
Not a subscriber?Click to get the print magazine.