This item has been supplied by a forage marketer and has not been edited, verified or endorsed by Hay & Forage Grower.
Companies purchase scales because the value of goods entering or exiting a facility is based on their weight. Without assured scale accuracy a company can lose thousands, if not hundreds of thousands of dollars annually.
Depending on the requirements and type of weighing device, annual maintenance costs for a truck scale run anywhere from $1,000 to $3,000. If one compares that to the potential cost of weighing errors, most users find that a good scale maintenance program more than pays for itself; oftentimes it also pays for the actual cost of the scale.
To be most effective, a scale maintenance program must have five key components: use of a state-licensed service provider; conducting calibration using state-certified test weights with written calibration and test report for proof of accuracy; a thorough testing process; visual inspection services and minor repairs; and thorough reporting.
Calibration is the key component of periodic maintenance
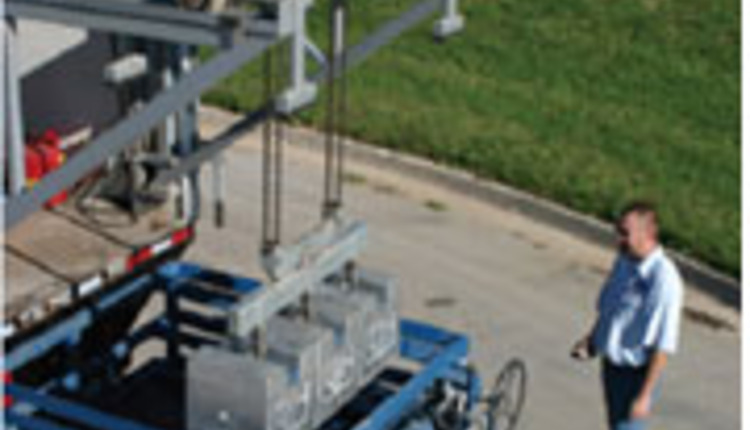
After a scale is installed, it is tested by the governing state’s weights and measures organization. This test ensures the scale’s commercial accuracy and protects the scale buyer, scale seller, and scale installation company. Upon state approval, the scale is certified and open for weighing.
However, it is important to understand that this initial calibration does not come with a guarantee for continued accuracy. Calibration can never be guaranteed, because accuracy is highly dependent on the way a scale is used and cared for. Weather, use, and wear are just a few of the factors that can change the accuracy of a weighing device. That is why periodic calibration is so essential. Test frequency depends on a variety of factors, including:
• Number of weighments per day
• Price of the product being weighed
• Number of days the scale is used annually
• Acceptable error rate
What’s the potential loss from a poorly calibrated scale?
Seemingly minimal errors can substantially cut into profits over time. Take the Acme Aggregate Company example shown below, in which two hundred pounds may appear miniscule, since a typical truckload of sand or gravel can exceed 80,000 pounds. However, when one does the math, the truth is revealed – an annual revenue variance of about $345,000.
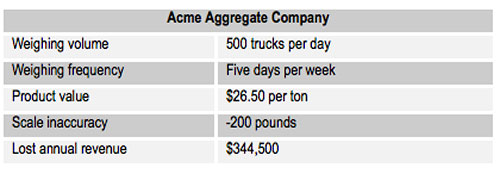
Five components of a good scale maintenance program
Use a state-licensed service provider
It is important to understand that the state weights and measures organization is the only entity that can issue a scale certification. A commercial scale company cannot certify a scale – but it does have the authority to recalibrate and reinstate an inaccurate scale that has been “tagged-out” by the state, as long as the scale company is state-licensed and registered in good standing. (Tagged-out means the scale has failed a state weights and measures accuracy test, so the state has attached a lockout tag to the scale, rendering it unusable for commercial trade.) So make sure the commercial scale company you are using shows you their valid license.
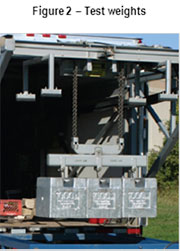
Calibration must be completed using state-certified test weights. An established scale service company typically has its entire inventory of test weights tested and certified annually, in accordance with state weights and measures standards.
Beware of service companies that test only a portion of their overall weight inventory each year. Preparing the weights and delivering them to a metrology laboratory for testing requires an enormous amount of time and money, so it may be tempting for some service companies to skip this important step. All too often, weights may be condemned and un-certifiable. This is why it is important to verify with your service provider that their weights have been certified.
Here’s a tip for conducting this test weight verification: All test weights have a stamp provided by the governing state weights and measures entity. It is also common practice, among companies that value quality, to request a copy of the test weight certification from the scale service provider. Weight serial numbers will be present on the certifications, and the customer can verify these numbers against the serial numbers on the test weights used by the service company.
Make sure testing process is thorough
To test a weighing device properly, one must first determine the length of the platform and the total number of sections along that length.
A scale section is determined by the presence of a load point, which is simply the location of a load sensor (also known as a load cell or strain gauge). Load points are where weight is transferred from the load to the scale and where scale accuracy is maintained.
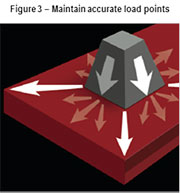
It is of critical importance, and mandated by the testing procedure of National Institute of Standards and Technology’s (NIST) Handbook 44, that the accuracy of load points are maintained, so as weight is applied, it is transferred evenly. If a load point or section fails a strain test, then it must be calibrated to conform to requirements by making a mechanical or electronic adjustment.
The load point is not calibrated to a certified weight, but rather calibrated to ensure that all sections weigh exactly the same or within government specifications outlined in Handbook 44 and/or issued by a state-sanctioned weights and measures organization.
Incorporate visual inspection and repairs
Like vehicle owners, scale owners must perform regular maintenance. In addition to the critical calibration component, a thorough scale maintenance program must include visual inspection, followed by any necessary repairs. A good service company should conduct a free visual inspection and have the ability to perform these minor repairs while on-site for the maintenance visit.

The visual inspection should include these key items:
• Scale condition
• Regulatory conformance issues
• Any damages
• Safety
• Clearance
• Grounding
• Mud/debris build-up
• Use issues
• Corrosion
• Electrical conditions
A reputable service company will carefully inspect the scale, looking at these and other items, and offer solutions to any issues discovered.
Most scale owners understand that it is better to repair and address issues when they are small, rather than wait until they are big and expensive.
Thorough reporting
A good scale maintenance program will provide thorough reporting. Each maintenance inspection should include a written report documenting test results, and including both before and after calibration, as well as a summary of finding and recommendations.