Large square balers have come a long way over the past 40 years of their existence. Improvements like larger sizes, better performance on wet hay, and weight and moisture sensors have added precision and efficiency to the balemaking process.
Enter the high-density baler as one of the newer innovations to big square baling. These machines compete with conventional and extended designs to help farmers make fewer bales from the same amount of hay. High-density balers can save producers money, but there are some factors to consider before making such an investment.
Crops and climate
In a recent issue of Vita Plus’ Forage Foundations, Kevin Shinners explains that compared to their 3x4-sized conventional counterparts, high-density balers reduce the number of bales made by 32%. This not only impacts the cost of baling, but the number of bales handled is an important factor in the cost of gathering, transporting, storing, and feeding hay and straw.
Hay and straw can both be packed into high-density bales, but it may not be necessary for the former. Shinners, a biological systems engineering professor with the University of Wisconsin-Madison, points out that engineers have determined optimum bale density to be 15 pounds per cubic foot, and different crops have different abilities of meeting this criterion.
“Consider the crops you bale,” Shinners asserts. “Density goals can often be met when baling alfalfa with an extended density baler. However, if straw is an important crop baled, high-density balers could be economically viable.”
Another factor to take into consideration is climate. It is recommended that large square bales be made at less than 16% moisture. This is especially important for high-density bales because there is more substrate to encourage microbial activity and heating. Humid conditions can make it difficult to attain these levels, and high-density bales will benefit from treatment with propionic acid, according to Shinners.
Parts and price
The next thing to think about is price. High-density balers can cost up to 50% more than a conventional one of similar size. This is because high-density balers must maximize chamber convergence and length for greater back pressure and compression forces to make their bales. Doing so requires more expensive parts.
“Greater compression forces require a larger gearbox, stronger plunger, and more robust drivelines and frame members – all of which contribute to a greater retail list price for these balers,” Shinners informs.
High density requires high intensity, and these balers require large tractors with high horsepower capabilities to operate. Even after the bales are made, they also need stronger support in the form of twine with greater tensile strength.
High-density balers can be attractive because of their ability to cut production costs. Even so, Shinners urges producers to carefully consider their specific situation to determine if these machines are right for them.
If you are currently using a 3x3 conventional baler, moving to a 3x4 baler might be a good first step to reduce handling and transport costs. Such an upgrade will reduce bale numbers by 34%.
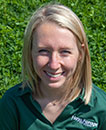
Amber Friedrichsen is serving as the 2021 Hay & Forage Grower editorial intern. She currently attends Iowa State University where she is majoring in agriculture and life sciences education-communications with a minor in agronomy. Friedrichsen grew up on her family’s diversified crop and livestock farm near Clinton, Iowa.