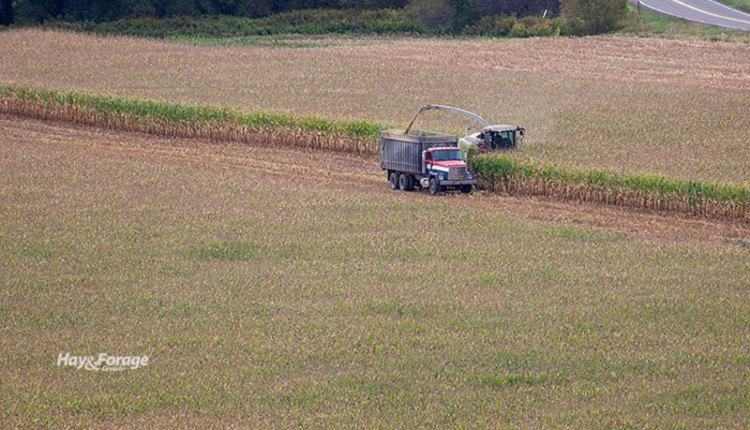
Editor’s note: This is the first of a two-part series on executing a successful corn silage harvesting season. Part 2 will appear in next week’s issue of eHay Weekly.
Most everyone knows how corn should be harvested and stored to ensure the best possible performance results when it is fed. So, why do we have train wrecks every year from the standpoint of excessive dry matter losses and spoilage?
According to Mike Brouk, it’s because there was never a silage plan developed, or if it was, nobody took ownership of that plan.
“A silage plan is critical and ideally starts at the end of the current chopping season for the next year,” said the Kansas State University extension dairy nutrition specialist. “You need to evaluate what went right, what went wrong, and what needs to change for next year,” added Brouk while speaking at a forage field day in Beresford, S.D.
“There needs to be an understanding of who’s doing what job,” he emphasized. “Who owns the plan? At the end of the day, someone must be responsible for developing and executing the plan. Someone has to have the authority to check things like kernel processing and initiate a change with the harvester if it’s inadequate. Someone needs to be in charge and monitor things such as packing effectiveness. Often, there is a plan but nobody ensures that it’s being followed. If 10 to 20 thousand tons of silage gets put up wrong, it can become really expensive,” he added.
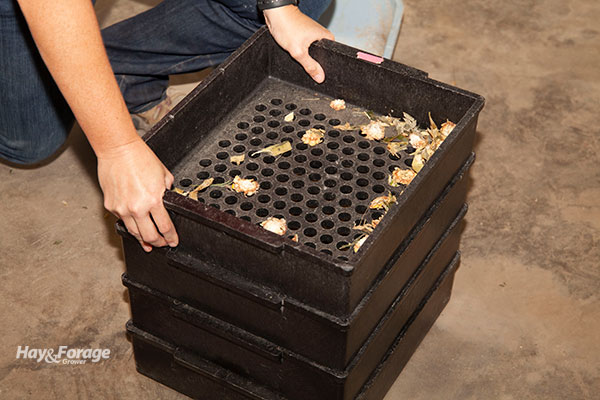
Chop it right
When chopping corn for silage, Brouk encouraged attendees to be thinking about both the animal and the machinery.
“We need fiber in the ration to stimulate rumination,” he said. “It has to be physically effective fiber; this is more important for dairy than beef animals. If fiber particles are too long, animals sort those pieces out at the bunk. If particles are too short, that’s not good either. To stimulate rumination, we need pieces that are about 2 inches long.”
When using a kernel processor, Brouk suggested producers can extend to about a 3/4-inch theoretical length of cut. If not running a processor, then a 3/8-inch length of cut is more appropriate to help do more kernel damage.
One way to gauge the job you’re doing is to use the Penn State Particle Separator. “If there are other forage types in the ration, then you can get by with about 3% of the material that stays in the top box,” Brouk said. “If corn silage is the sole forage source, then about 8% of the sample needs to be on the top box. In both cases, there should be less than 5% fines on the bottom pan,” he added.
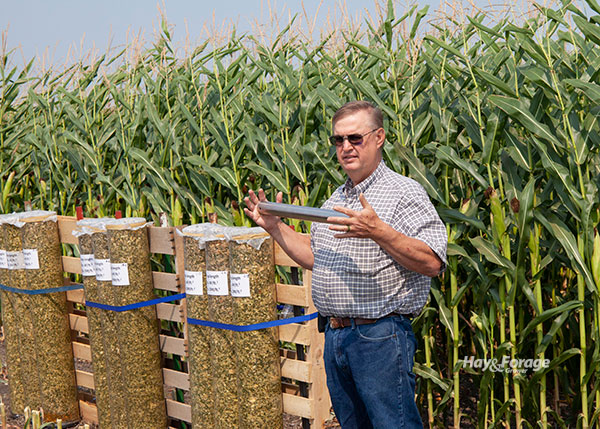
Keep what you harvest
“Some silage losses are avoidable and some are unavoidable,” Brouk stated succinctly.
One unavoidable loss is plant cell respiration after the crop is chopped. This process produces heat, and that equates to a loss of dry matter. Fermentation losses are also unavoidable and can range from 2% to over 4% because bacteria require energy to reproduce. “So, right off the bat we’re looking at between 4% and 8% losses,” Brouk said.
Leaching of nutrients in effluent is an avoidable loss and simply requires silage is harvested at the right moisture level. Secondary fermentation when we feed out, or face loss, is largely avoidable and the same can be said for feedout losses.
“Total silage dry matter losses can range from 8% to over 40%, and in my experience, it’s not uncommon to see about 15% loss on many farms,” Brouk related. “I think we can do better than that.”
Densely packed silage is critical in terms of reducing dry matter losses. Brouk pointed to one study where silage that was packed at only 10 pounds per cubic foot lost about 22% dry matter. Most experts recommend packing to at least 15 pounds per cubic foot of dry matter, which in the study resulted in about a 16% dry matter loss. Packing to 20 pounds per cubic foot, which is likely not realistic on most farms, resulted in only a 10% loss of dry matter.
“Getting density up is critical to exclude air, which is your enemy,” Brouk noted. “If packing is inadequate, the silage will heat more and fermentation will be delayed. Moisture impacts our ability to get a good pack. If the silage is dry, it will pack like a dry sponge,” he added.
A second way that inadequate packing will ultimately depress livestock performance is during feedout. Air infiltrates the face and a secondary fermentation takes place. This allows molds and yeasts to start growing. The dairy extension specialist emphasized that minimizing days of exposure and having a good pack are critical to keeping dry matter losses in check.
“Energy is neither created nor destroyed,” Brouk explained, “But it is transformed. When air intrusion becomes a factor, we’re transforming feed energy into heat energy that is lost to the environment. That loss is comprised of the most digestible nutrients in the silage.”
Next week: Moisture, kernel processing, and packing