This item has been supplied by a forage marketer and has not been edited, verified or endorsed by Hay & Forage Grower.
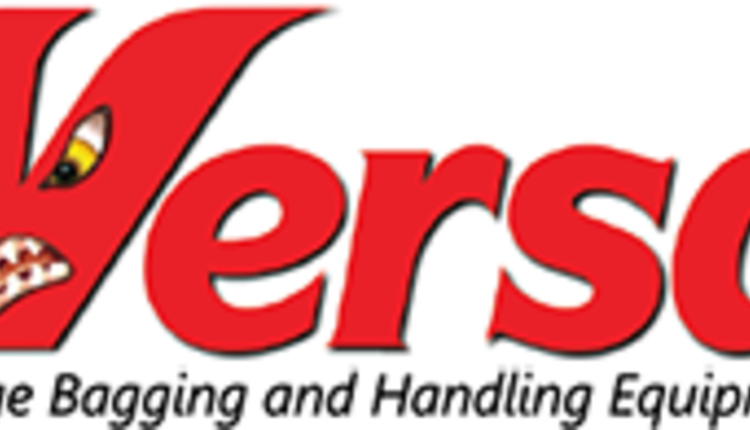
For farmers with livestock such as dairy cows and beef cattle, dietary supplementation with dry grains has traditionally been utilized as an economical way to meet the high energy demands of the herd, particularly when forage is scarce or of low quality. However, farmers are increasingly turning to high moisture corn silage, specifically snaplage/earlage, due to its high energy content and easy digestibility. In many ways these high energy “concentrates” can almost match the nutritional energy of dry grain pound for pound.
Dairy cows, particularly those in peak lactation, have very high energy demands. For beef cattle, particularly those in the finishing phase, high energy is also needed for rapid weight gain and marbling of the meat. The practice of harvesting the entire corn plant, chopping it up while still green, and fermenting it creates high moisture silage that serves as superior feed due to its excellent energy density. To support optimal milk production and overall animal health, dry grains are often mixed with silage, hay, and other feed ingredients in a Total Mixed Ration (TMR) to ensure a balanced intake of energy, protein, and fiber.
Now, a growing number of farmers are utilizing snaplage/earlage as an alternative to dry grain supplementation.
Snaplage/earlage, which involves the entire ear, including cob, kernels, husk and part of the shank, is harvested and ensiled at 32-40% moisture.
One of the main obstacles of producing such high moisture silage using traditional methods like piles, pits, and bunkers is the considerable risk of spoilage and loss, which can amount to as much as 30%. This combined loss is often referred to as “shrink”. The problem with these conventional silage storage methods is the excessive exposure to oxygen, which leads to rapid silage deterioration. The standard practice is to leave the open face of the pile, pit or bunker open for feeding. This leaves hundreds of square feet exposed and deteriorating before it can be fed
This storage challenge is leading farmers to store snaplage/earlage in silage bags instead of conventional methods. Bagging provides ideal conditions that minimize spoilage. With silage bagging, the oxygen is removed almost instantly, and fermentation begins promptly. The sealed bags protect silage quality and maintain favorable fermentation conditions even amid unfavorable circumstances such as exposure to rain, moisture, excessive dryness, or prolonged storage.
“My experience is that high moisture corn generally does better in a bag than in a bunker or a drive over pile,” says Dr. Keith A. Bryan, Technical Service Manager Silage and Dairy, North America, for global biosolutions company Novonesis.
Proper silage packing ensures the removal of oxygen and protection of the bag for snaplage/earlage. This results in higher nutrient retention per acre, increased milk production, enhanced weight gain, improved herd health, and reduced veterinary costs.
The proper bagging of snaplage/earlage can also help to streamline operations. High moisture snaplage/earlage can be part of the normal corn harvest. Simply cut a smaller portion of your corn crop using a snapper head on the harvester. Bag that portion in separate, smaller bags and then mix together with the larger, whole plant corn silage instead of dry grain when mixing your ration. This saves a significant amount of time and money since it eliminates the need to purchase dry grain from outside sources.
A farmer by trade, Ryan Williams of R & M Cattle Company in Farwell Texas, operates his own feed yard, a small dairy, and custom harvests forage crops for similar nearby operations in the area. Williams, who has bagged silage and forage since 2006, says the technique works particularly well for well on lower tonnage crops like high moisture corn.
“The shrink is very low, about 1 to 2%, and the quality of feed is the best when bagged because it’s totally protected. There’s no mold, there’s no crust on top, none of that,” says Williams. “You can keep the bag for quite a while until you need to use it. You can use some of it and stop.
We’ve had silage [remain in bags] for three years before it was used,” adds Williams.
Bags provide another advantage. High moisture corn silage like snaplage/earlage stored in silage bunkers, bags, or pits can be susceptible to pest infestations if not properly managed. The warm, moist environment is ideal for rodents to nest in and for birds to scavenge food. The fermentation process that high moisture corn silage undergoes enhances its smell and taste, making it even more attractive to pests.
The effective use of silage bagging, however, allows for a smaller feedout face and less exposure to the environment, including pests.
“With the large bags the feedout face is so much smaller and you go through a bag so much quicker than a huge drive over pile or bunker,” says Dr. Bryan of global biosolutions company Novonesis. “If packed correctly and by feeding it out more quickly, oxygen penetration is reduced, and you can have more hygienic feed in terms of reducing yeast and molds…compared to a bunker or a pile.”
“The amount of high moisture corn that is exposed to rodents and birds is also quite a bit less in a bag than it is in any other storage form relative to the total amount stored,” adds Dr. Bryan.
Optimal Bag Packing Density
To maximize the effectiveness of their equipment, farmers should prioritize packing pressure as a key factor to consider for equipment selection. With proper silage packing and bagging, the oxygen is removed almost instantly, and fermentation begins promptly. The sealed bags protect silage quality and maintain favorable fermentation conditions.
Among silage bagging equipment, packing is approached in various ways, which can affect productivity. One bagging system utilizes a cable system with a heavy net backstop. With such a system, after each bag is filled, the cables must be rewound and the backstop moved to the next location, a cumbersome process.
For greater efficiency, Astoria, OR-based Versa Corporation, a global leader in agricultural silage bagging and handling, created an innovative cable loop density system that uses a single adjustable cable inside the bag. The OEM also developed a heavy-duty belt system that facilitates tighter packing of longer silage bags than the industry norm, which minimizes air pockets and spoilage while maximizing storage capacity.
“The goal is to firmly pack the bag without over-stretching the bag while gradually moving the machine forward as the bag fills,” says Steve Cullen, President of Versa.
Today, the process of creating bagged silage for dairy farmers is relatively simple. Essentially, they back up a truck, dump the feed in, and start bagging. Capacities generally range from 2-5 tons per minute for side unloading wagons to higher capacity truck rear-end loading models that handle from 4-16 tons of bagged silage per minute.
The largest model the OEM offers can switch between 12 and 14 bags as part of the machine design and can be easily transported to different sites due to a narrow 12’ width.
About 15 years ago, Williams says R & M Cattle Company switched to a Versa bagger in part because it was easier to maneuver and maintain. He also appreciated that the equipment is “farmer friendly” without complicated controls and hydraulics.
“Our bagger is easy to maintain; there are few specialty parts on the machine,” says Williams.
For more information, call (800) 837-7288 or visit versacorporation.com.